Planning for Project Failures- The Importance of Strategic Planning
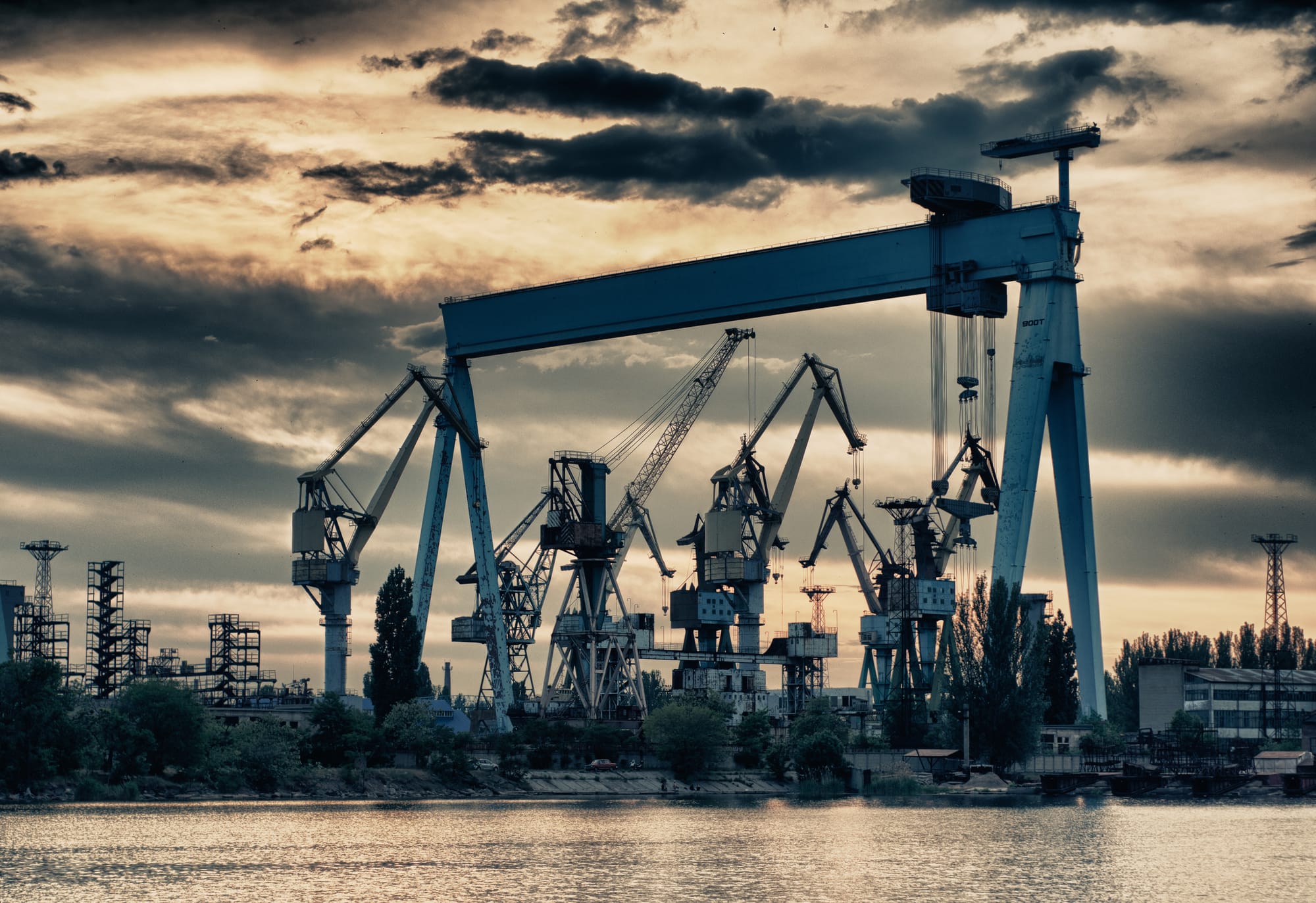
It has often been said that the key to project success both lives and dies with the ability to effectively plan. When managers think of project planning, their mind tends to gravitate toward a mixture of resource allocation, budget, and schedule among many others. Our ability to effectively juggle these areas will often define our project. While it is always in our best interest to plan effectively, failure to identify and plan for project failures can just as easily sink our project if due diligence is not paid toward this important objective.
Join us here at GovGig as we discuss the importance of planning for project failures on your federal construction project, and how this concept can help to shape the overall success of your Federal contract.
So, what exactly does it mean to plan for failures? What we are not referring to is planning to fail. The concept of planning for failures is proactive in nature in that effective processes are established that aim to identify trends before they become problematic. Not only does it aim to identify potential project challenges, but an effective plan will also incorporate contingency planning into your management practice. Consider the following important steps as we outline this important process:
- Proactive Measures Through Strategic Planning- In the world of strategic planning, marketing, stock market analysis, and yes, even within construction management, the concept of leading indicator analysis is a BIG DEAL. Leading indicators refer to data and trend analysis which aims to identify trends before they negatively impact your organization. Just as an Economist analyzes market data to identify how it will affect stock prices, you must analyze trends in your project to curb challenges before they become failures.
As an example, from a safety management perspective, leading indicators are often utilized by assessing the overall health of the project through safety inspections, employee training, AHA review, and development, or even through the types of hazards abated on your project. Each of these tasks ultimately has two primary goals in mind, to identify the project’s challenge areas, and to mitigate these challenges before they result in a project-related incident.
Leading indicator assessment is not limited to safety management but is also a necessary part of maintaining quality assurance and executing a well-run and efficient project. In essence, it's about taking a proactive approach, strategically setting your objectives, and pinpointing trends before they lead to project setbacks.
- Contingency Planning- Federal construction projects can often be complex and challenging. Because of this, focusing on contingency planning in the event of project failures becomes a necessity. Often, no matter how much effort we put into planning, failures on your project can and will occur. Unforeseen weather conditions, supply chain disruptions, design changes, or even accidents can cause delays, increase costs, or compromise safety. That's where contingency planning comes into play. It's a proactive strategy that will prepare your team for unexpected events, ensuring your project stays on track, and within budget, all while maintaining the highest safety standards. Contingency planning involves identifying potential risks that could disrupt your construction project and developing strategies to manage and mitigate each of those risks. The objective is to minimize the impact of unforeseen events on project timelines, budgets, quality, and safety. Consider the following key steps toward establishing effective contingency plans for your project:
- Assess Your Risk- You must identify all possible risks that have the potential to disrupt your project. This might range anywhere from significant weather delays to equipment failures, to challenges with labor to workplace injuries.
- Develop of Plan- Once you have identified your potential risks, develop a contingency plan for each risk. Your plan should outline steps to take when this risk occurs and should focus on minimizing the impact that it places on your project. Your project team should be trained on contingency plan execution to ensure that your team is adequately prepared if the potential risk does occur.
- Allocate a Contingency Budget- You must set aside a portion of the project budget to cover potential costs associated with each risk event. This budget should be based on a realistic assessment of the potential financial impact of each identified risk.
- Continuous Assessment- Continually monitor and review your contingency plans. As the project progresses, new risks may emerge, and existing plans may need to be updated.
- Learning from Failure- Remember, as project failures occur, this will allow you to assess ways in which you can prevent these failures from occurring in the future. Following a workplace injury, for example, an incident investigation is often performed focused on identifying the root cause of the injury and potential corrective action to prevent recurrence. This same type of process should also be followed should your project experience significant failures. Ultimately, it is essential that you learn from past mistakes and that noteworthy strides are taken that will allow you to turn those significant setbacks into long-term success.
Feel free to reach out to our team here at GovGig if you want to learn more about the value of planning for project failures and how you can best execute this important concept on your federal construction project.
Cory J. Grimmer, CSP, CHST