The Control of Hazardous Energy (LOTO)
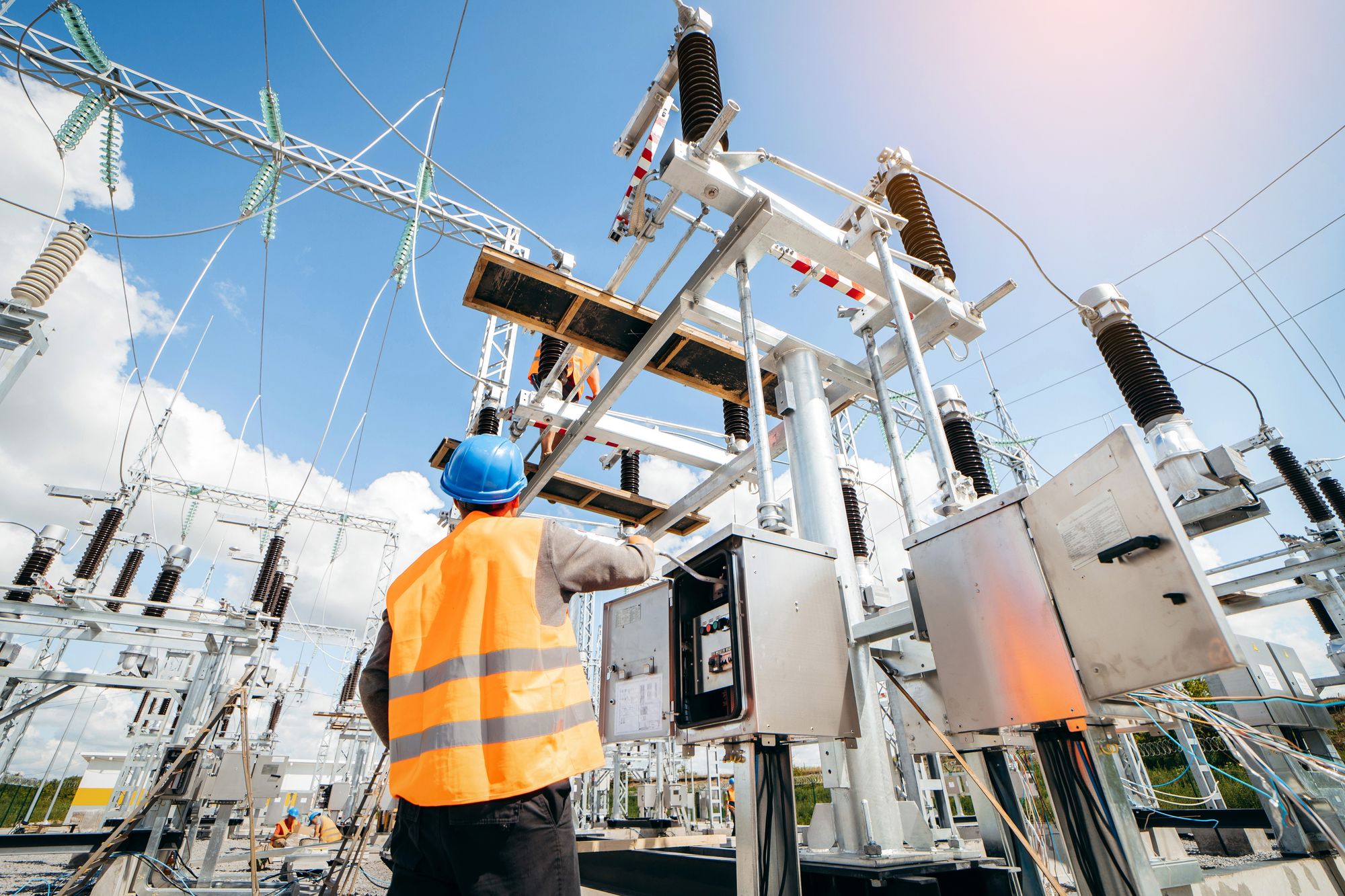
A GovGig EM 385 1-1 Compliance Article
Ensuring the safety of our employees, subcontractors and clients under our command is an imperative here at GovGig. We truly understand the challenges that work around hazardous energy can pose to our work groups and continuously strive to ensure that sufficient controls are established to protect us from harm.
Hazardous energy can come in many forms. Whether you are working around potentially energized electrical systems, mechanical energy from moving parts near machinery or equipment, hydraulic energy or even pneumatic, the goal should be the same. Steps should always be taken to limit risk to its lowest acceptable level (residual risk) through pre-job planning with safety in mind and through establishing controls to protect our workforce from potential exposure. Planning here is key as failure to properly plan and control the unexpected release of hazardous energy may come with devastating consequences. When hazardous energy is not properly controlled, it can result in serious or even fatal injuries. Injuries may include electrocution, burns, crushing, cutting, lacerating, amputating, or fracturing body parts, and others. (OSHA.Gov)
Due to the serious nature of hazardous energy, please take the time to thoroughly plan your work. Be familiar with the requirements outlined below and take steps to ensure the safety of those under your charge.
As required under EM 385 1-1, Section 12, whenever there is potential for exposure to hazardous energy, specific steps must be taken to ensure that work tasks are planned, and controls are identified and established to perform this work safely.
The Control of Hazardous Energy is outlined under Section 12 of EM 385 1-1 and dictates the following requirements:
Planning Stage:
1. Development of a Hazardous Energy Control Program (HECP) is required when potential exposure to hazardous energy is present as part of the scope of work. This document is to be submitted as part of the Accident Prevention Plan. (12.A.01) The HECP is designed to “clearly and specifically outline the scope , purpose, authorization, roles and responsibilities, rules and techniques to be used for the control of hazardous energy.” (12.B.01) When developing a HECP for your scope, ensure that the requirements outlined under section 12.B for this submittal are closely followed as failure to ensure thoroughness within this program may result in untimely delays due to the program not being accepted.
2. In conjunction with the HECP, Hazardous Energy Control Procedures (HEC) must also be developed and submitted as part of the AHA process. Employees must receive training in the elements of the HEC (12.C). This training must be documented. In addition to initial training, retraining may be required in the event of a change in process, or if through inspection, “there is reason to suspect the presence of, inadequacies in or deviations from the employee's knowledge or use of HEC procedures.”
3. Remember, before any work involving hazardous energy can be performed, your work task must be assessed for pertinent hazards and HEC clearly identified. Relevant hazards will be assessed and controls established via an Activity Hazard Analysis or AHA. As we have discussed in previous publications, the AHA allows for us to assess our work by breaking down our work tasks into steps, identifying hazards associated with each step, and then implementing controls to ensure that the risk associated with that task is at an acceptable level.
Execution of Work
Once work has been planned and controls have been identified, steps must then be taken prior to beginning work tasks to isolate and control hazardous energy.
As specified under Section 12.D.03, “All equipment shall be covered by the HEC procedures and all energy sources shall be controlled before performing servicing, maintenance, testing, installation or removal on equipment in which the unexpected energizing, startup, or release of stored energy could occur and cause any of the following: Personal injury, property damage, loss of content, loss of protection, loss of capacity, or harm to the environment.”
It is essential that prior to the beginning of work activities that all sources of energy are:
1. Identified and controlled, and
2. All sources of potential hazardous energy are verified to be in a zero-energy state prior to beginning of work.
Control of hazardous energy can be accomplished through several methods. This may include implementation of Energy Isolating Devices such as Lockout Tagout (LOTO). These devices are mechanical devices that, when utilized or activated, physically prevent the unplanned transmission or release of energy…” (12.D.01.a). As there are diverse ways in which hazardous energy can be isolated, we will not be covering each scenario. Be sure to familiarize yourself with the specific method of energy isolation for the system in which you are working prior to establishing your HEC Procedure.
Please note that sole use of a tagout system for all types of equipment is not acceptable under the EM 385 1-1 Standard. Systems that are capable of being locked out (LOTO) shall be locked out. If the system is not capable of receiving a lock, then a tagout system may be utilized; however, the system being implemented must provide full personnel protection.
A zero-energy state refers to the point at which equipment has been safely isolated from any chances of re-energization or release of residual energy. Verification methods will depend upon the system/equipment in which you are working. Typical methods for zero-energy verification may include methods such as attempting to turn on equipment, attempting to actuate a valve, or verifying zero energy through electrical testing among others.
Inspection of process and verification that controls are adequate must not be forgotten. Remember that changing work practices in the middle of your work may not be sufficient. In the event of HEC deficiencies, stop work, reassess controls, amend your written procedures, and train your workers to the new process.
If you have questions or concerns regarding this process, do not forget to coordinate with your GDA point of contact. As always, feel free to reach out to us here at GovGig should you have any questions or need support relating to what can be a very challenging process. We are here to support you as you work through the many challenges of Federal Contracting. Let us build a better, stronger, and safer tomorrow together.
Cory J. Grimmer