The Importance of Stop Work Authority
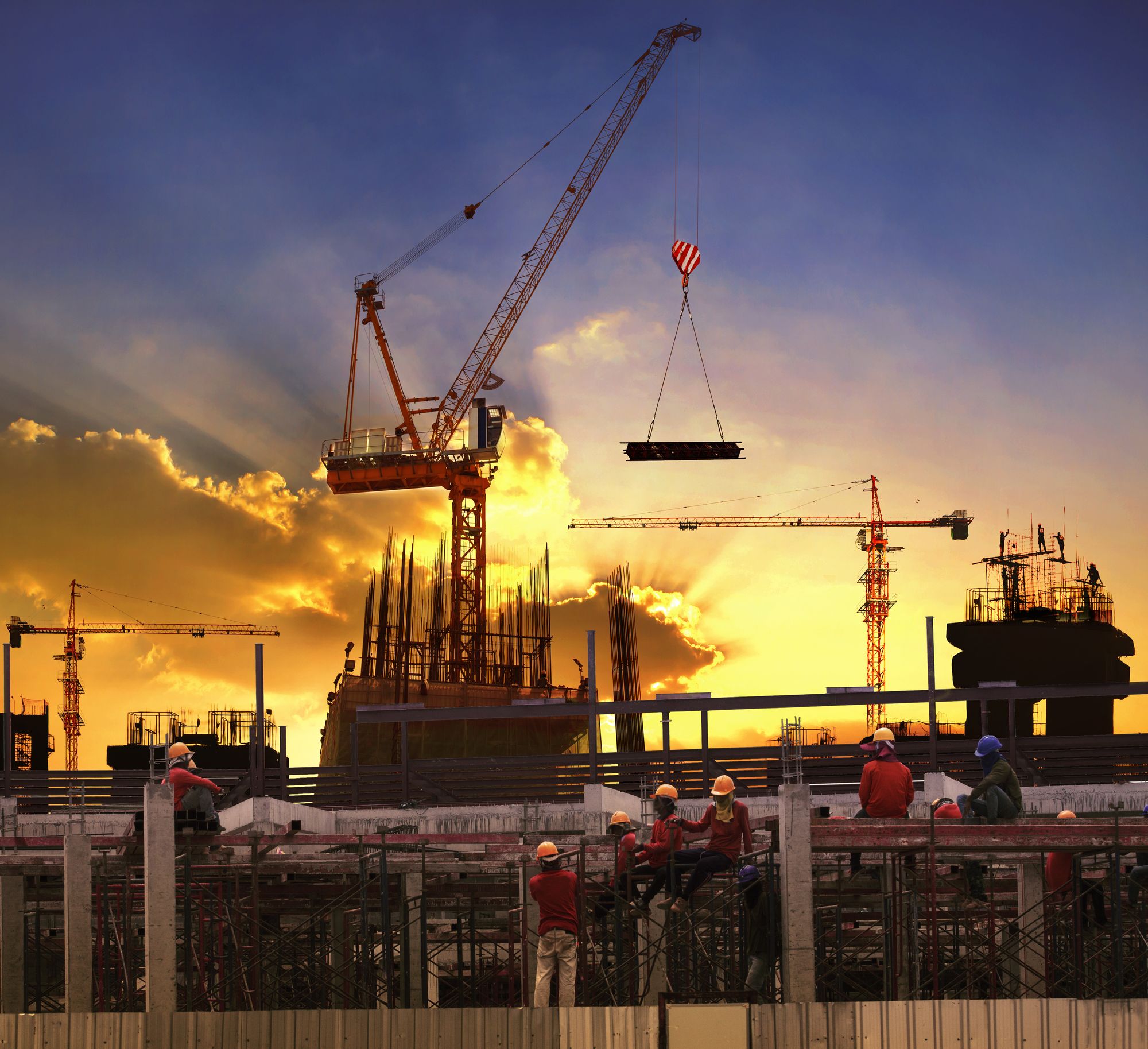
A GovGig EM 385 1-1 Compliance Article
Stop Work Authority (SWA)- You may have heard this term quoted a time or two if you have spent any amount of time in the industry. As the importance of workplace safety has gained a significant foothold in the way in which we plan and execute our work, the SWA process has become commonplace across many organizations over the past few decades.
The concept of stopping work has become an expectation for all work activities where unsafe acts or unsafe conditions exist. In simple terms, SWA provides a process for all workers where they are given the responsibility, right, and obligation to stop work when imminent danger to themselves, others, or the public exists.
While briefly mentioned, although not specifically outlined under EM 385 1-1 nor under OSHA, it is both identified and supported under US regulation. In an article written by Scott Gadis Titled Stop Work Authority: A Principled-Based Approach, he describes the value of Stop Work Authority and how a US Supreme Court ruling defined this right under US Law. He states:
“Under federal law in the United States and similar laws written in other countries, employers must provide employees with a safe and healthy workplace free of recognized hazards. Workers have the right to refuse to perform dangerous work and, if they do so, are protected against employer retaliation.
The law was supported by the courts on Feb. 26, 1980, when the U.S. Supreme Court issued a ruling that defined—with great clarity—a worker’s right to refuse work when there was a reasonable concern that death or serious injury or illness might occur performing the job. This decision stemmed from a 1974 case against Whirlpool Corp. in which two workers refused to crawl out on a screen from which a co-worker had fallen to his death only nine days earlier.
The two workers in the Whirlpool case were ordered by management to go out on the screen 20 feet above the floor to retrieve small appliance parts that had fallen from a conveyor belt system above. The screen was in place to protect workers in the plant from falling parts. Claiming that the screen was unsafe to climb, both employees refused to carry out the task and were sent home for the day and denied pay.
It is supported by law: If an employee believes working conditions are unsafe or unhealthful, he or she has the right, the responsibility, and the authority to halt work activity without fear of retribution.”
The SWA process itself is extremely critical. Workers need the confidence and authorization to be able to stop work when they feel that work conditions are unsafe and to do so without fear of retribution. For some companies, SWA can be formal and documented, for others, this process may be informal. Regardless of which is used, the SWA process is similar in its application and typically includes the following important steps:
1. Stop Work Intervention- When a perceived unsafe act, condition, or area of concern is identified, or should workers have a lack of understanding in a task that may result in an incident, a stop work intervention is initiated with the at-risk party. Within this intervention, the work process is immediately halted until a resolution can be achieved. If necessary, work should be stopped with all processes involved including removal of personnel from the work area in an effort to make the area as safe as possible.
2. Notify Without Fear of Retribution- Affected workers in addition to project supervision should be notified of the intent to stop work. It is essential that this process be performed without fear of retribution. Should workers fear retaliation, the likelihood that unsafe acts or unsafe conditions will be addressed will be greatly diminished.
3. Investigate- Affected personnel will review and discuss the situation and come to an agreement on the stop-work action. If all parties come to a consensus that it is safe to resume work without modifications, work may proceed. If the stop-work initiated is valid, corrective action must be identified and implemented prior to proceeding with work. While not required, it is highly recommended that contractors document this process.
4. Correct- The conditions or actions that pose a threat or imminent danger must be corrected before work will resume. Work process modifications, repairs, or any additional corrective action that has been identified will be implemented to the satisfaction of the concerned body. Until all reasonable concerns have been addressed, work shall not resume.
5. Work Commencement- Once the issue identified during the SWA process has been inspected, assessed, and addressed to correct hazards present, work may resume. It is essential that the process does not end here as continuous monitoring and communication is necessary to ensure that the SWA concern has been completely addressed and that controls are effective and adequate to protect workers.
In addition to the act of stopping work itself, perhaps the most necessary requirement in the SWA process is that workers MUST be empowered to speak up. For some, speaking up can often be intimidating. Inexperienced workers may not feel comfortable bringing up perceived risk. Others may feel that their company may look unfavorably upon them for speaking up or that bringing up problems will result in conflict. Others may give in to peer pressure as a work crew may have been performing work a certain way and may not feel the need to change their processes.
Once again, workers MUST be empowered. Addressing unsafe acts and unsafe conditions must become the norm. As we empower our workers with this authority, and as we support their right to a safe and healthy workplace, we can move forward with confidence as we look to build a safe and successful project.
Please reach out to us here at GovGig should you need assistance or support in this area. We have the background and expertise to help as we work to meet this shared goal of a safe and healthy workplace for all.
Cory J. Grimmer, CSP, CHST
Health & Safety Consultant, SSHO